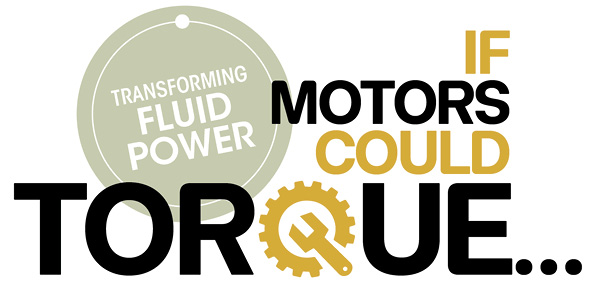
Fluid power has become a vital component in our ability to perform work: it harvests our crops, takes our waste to the landfill, moves the landing gear, entertains and protects us, and all with a power density and flexibility that is unmatched in any other power transfer system. However, when it comes to efficiency, fluid power systems are not very high on the list. This article series will ask us to think differently about our fluid power systems. We will look at energy in a different way and discover ways to transform fluid power energy to make our systems more efficient, and then be able to make better use of the new and improved components available to us.
I know, I know… the title is a bad pun, but it actually helps me get the point across. If motors could torque, in other words, if fluid power motors could sense the torque needed and draw only the energy units needed to supply that torque, we could produce some very efficient systems.
We have been talking about referring to volume, flow, and pressure as energy units or units of power instead of separating them in our design thinking. We have raised the question of finding a way to transform the energy units in a way that would be most efficient and not force us to use more than is necessary. As it turns out, we actually already have a way of doing this with hydraulic motors. In a closed-circuit hydrostatic transmission, we routinely have a system where the pump transforms mechanical energy into hydraulic energy consisting of volume and pressure at some flow rate. The motor then transforms hydraulic energy back into mechanical energy. There is no restrictive flow control. Almost all the energy transformed by the pump is not only available but is totally used up by the motor. As a matter of fact, the only energy put into the fluid is what is demanded by the needs of the motor, plus the internal leakage and demands of the charging system.
So, did I write all this just to say we need to use more hydrostatic transmissions? No, but the transmission will be a good place to start in our search for more efficient transformers.
An electric motor has a specific winding and is powered by a specific voltage at a specific frequency. The result is a specific RPM that changes very little with the load. For example, a typical motor operating at 50 Hz, wound for 1550 rpm, and equipped with a grinding wheel will have a high resistive inertia load. When the motor is started, there is a major inrush of current as the motor tries to leap from zero to 1550 rpm. When the RPM is attained, acceleration stops and the motor coasts at the prescribed RPM. The amperage drops dramatically but never drops to zero because there will always be some energy required to keep the motor running, even with no load. The voltage, frequency, and windings do not change; only the amperage changes. When an operator begins to sharpen a tool, there is a new load on the motor but the motor maintains its RPM.
This motor has only one variable: the amperage, but it is able to use that one variable to draw only what is needed from the power grid to maintain … to maintain what? Not the torque, not the power, but the RPM. The electric motor is programmed by its structure to maintain an RPM when there is a constant frequency and voltage supply. Only the amperage (flow) changes with the torque load.
So, the question is: How can we construct a hydraulic motor to respond in the same way as an electric motor? Can we make it so that, with everything else being equal, only the flow changes with a change in torque? Of course, we can! And we already do. We are simply describing a variable-displacement hydraulic motor. What we will do differently is control the motor using only RPM as the determining factor.
You may recall, or you can go back and look, that we discussed the rotary power formula: P = dpN / K where P = Power, d = displacement, p = pressure, N = RPM, and K = a constant. This formula will be the basis for our understanding of the ability to set RPM as our control.
We will replace the electric motor with a variable-displacement hydraulic motor being supplied by a variable-displacement, pressure-compensated pump with more than enough flow capacity for the work to be done. The default condition of the motor is maximum displacement. We will outfit the motor with a mechanism that will sense the RPM and control the displacement. (Exactly how we do that is for another discussion.)
Let’s see what happens: Fluid is directed to the motor, which is at full displacement, so we have maximum torque applied. The grinding wheel begins its leap from zero to maximum RPM. At 1550 rpm, the sensing control adjusts the displacement to the discrete point where the displacement and pressure provide the torque to maintain the RPM. When an operator begins to sharpen the tool, the new torque load causes the motor to try and slow down. The change in RPM is picked up by the sensor, and the displacement is increased so that the new torque can be applied.
Wait a second! It happened again. Are you trying to tell me that increasing the displacement will cause the motor to speed up, and that decreasing the displacement will cause the motor to slow down? That is backwards. Everybody knows… Oh! I get it. Using the power formula, we see that, with RPM being constant, a change in torque means a change in power. The only way to get an increase in power with a fixed RPM and fixed pressure is to increase the displacement. The only way to get a decrease in power with a fixed RPM and fixed pressure is to decrease the displacement.
Let’s try it out: Get out your calculator again or open up a spreadsheet and plug in the power formula. For power, put in 2 kW and for pressure, 20 MPa. RPM is fixed at 1550, and K is 60,000. When we solve this for displacement, we get 3.8 cc.
An increase in torque at a fixed RPM will require an increase in power. So, increase the power to 5 kW. What do you get for displacement? That’s right. It increases to 9.7 cc. We did not change the pressure; we changed the flow. There is no restrictive flow control. The motor only drew the energy units (cc x p) to do the job. We parallel the function of the electric motor. We fixed the RPM and pressure, and then regulated the power by the flow without the use of a restrictive flow control.
We actually have an advantage over the electric motor. There is an absolutely discrete product of pressure and displacement for a given torque. The power formula shows us that maintaining a constant RPM will produce the correct displacement even as the available pressure changes. We can use energy stored in a gas accumulator and, without the need of a flow control, maintain a constant RPM. As the pressure in the accumulator is reduced, the motor displacement will increase. The motor is going to draw only the energy units it needs for the work.
How is this system different from a hydrostatic transmission? The most significant difference is that multiple motors can be operated from a single power source and each motor will only draw the energy units that it needs. It is conceivable that a facility that uses multiple electric motors with varying loads could determine the average power requirement and then install a central hydraulic power unit using an electric motor whose rating matched that average power. During low power usage, the energy would be stored in an accumulator system. The electric motors would be replaced with RPM-sensing hydraulic motors. Each motor would only draw the energy units needed for the task at the moment without restrictive flow controls. There could be substantial energy savings for the facility due to increased efficiency, lower demand charges, and better power factors. That is if motors could torque.